Why is the Indian Steel Industry unable to compete with China?
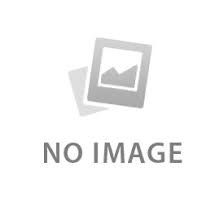
- Updated Wednesday May 29 2024
One of the most well known and frequently occurring phenomenon in the Indian Steel Industry is industry bodies complaining to the Steel Ministry and other concerned Central Government authorities about Chinese companies ‘dumping steel’.
What does dumping steel mean? What are the tariffs that are frequently imposed on these Chinese imports, and ultimately why does the Indian Steel industry have such a tough time competing with the Chinese producers?
Let us at the outset state two caveats. This phenomenon although accentuated in the steel market, is not unique to just the steel industry. Across numerous industries and baskets of goods from cellphones to automobiles to textiles, Indian homegrown manufacturers find it very difficult to compete with the Chinese manufacturers on pricing, and sometimes on product quality. Second, this is also not unique to India, which might actually be one of the countries that could almost be on par or the same league as Chinese manufacturing. Countries around the globe find themselves unable to compete with Chinese imports and have either reconciled to the Chinese imports or found similar safeguards to protect local industries.
China is the dominant force in the globe in terms of steel consumption and production. In 2023, it is estimated that China produced above 50% of the total global volume of steel production. Therefore there is no surprise that the steel market and the global steel industry is largely dictated by Chinese manufacturers. They are able to set benchmark prices, have tremendous global distribution and can win market share with ease given their economies of scale and other competitive advantages in manufacturing steel.
So what is steel dumping that occurs in India and why does India so frequently impose anti dumping duty on Chinese steel imports?
Dumping occurs when excessive manufactured goods are supplied at cost or at a discount to clear inventory and keep the manufacturing cycle rolling. How this works in practice is that when there is a consumption slowdown anticipated, manufacturers instead of cutting back on production reduce prices and offer their goods at market discounts, sometimes distorting the market rate itself. In effect the manufacturers choose to ‘dump’ the goods usually in new and foreign markets where they can have a devastating impact on local manufacturing as dumping does not usually stoke domestic demand but finishes domestic supply. As a safeguard against the cyclical dumping, Indian manufacturers lobby the government to impose high duties or tariffs on imported steel so that they can price the indigenously manufactured goods at par with the imports.
Now lets take a closer look at why China can outcompete almost all manufacturers on the global level in the manufacture of steel.
The main inputs required for steel manufacturing are raw materials which include iron ore, coking coal and others like Carbon, industrial gases etc., energy and the equipment and machinery within steel manufacturing plants such as blast furnaces, ovens, rolling mills, etc. which come be summed as manufacturing capital or 'industrial capital'. Other than these, there is also requirement of finance for capital expenditure and working capital, as well as distribution and logistics infrastructure to allow for efficient transport and distribution of the goods for better sales.
As far as raw material is concerned, compared to India, China itself does not have any competitive advantage in terms of iron ore reserves. This commodity is present in China, and published reserves of iron ore are around 6 billion tons. In 2022 coking coal production was around 600 million tons. While China has ample coal reserves it usually resorts to import for additonal coking coal which is necessary for iron and steel production. Compare this with India’s reserves of 5.5 billion tons of iron ore and coking coal production in 2022 of around 60 millions tons (almost 10% of China). So it is likely that the presence and production of coking coal might provide a slight advantage to Chinese manufacturers as Indian manufacturers have to rely on higher cost imports for a greater share of coking coal needs. However, more than the indigenously available raw materials, the major advantage of Chinese manufacturers is provided by access to foreign raw materials and minerals. Chinese companies are aggressive buyers of mining operations and/or output from mines that help them secure raw material supply at low cost basis. While some Indian manufacturers have been able to emulate this, poor access to capital and difficult foreign exchange regulations have hampered the access to foreign raw material.
Energy plays a major role in the production of steel as smelting and production are very energy intensive processes. In terms of energy availability and cost, average industrial rate of electricity in China as per some published reports is 8 - 9 cents per unit. In comparison India has significant energy availability, and most large steel producers also produce electricity, the average reported costs for industrial energy is around 7 - 8 cents per unit.
In terms of industrial capital, Chinese manufacturers have the largest capacity of production on the planet, and account for almost 50% of the total global capacity. Total Global steel production capacity at the end of 2023 was around 2500 million tons per annum. Chinese capacity was around 1300 million tons per annum - a whopping 52%. In comparison India has around 165 million tons of crude steel capacity which represents around 7% of total global capacity. Meanwhile total steel production figures indicate, global steel production at 1850 million tons in 2023, while China accounted for almost 1100 million tons (59.5%), India accounted for a mere 140 million tons (7.6%). While building industrial capital, there is a very strong case for economies of scale that allow organized capital expenditure to reduce per unit costs. Furthermore, the advantages also percolate while securing raw materials as larger buyers have greater bargaining power.
In terms of cost of capital, or simply put average interest rates for industrial projects we find that the average interest rates in China, benchmarked to the Chinese Prime Loan Rate is around 3.45% +. In comparison India has had historically very high interest rates which were at some point as high as 15% for what are considered safe industrial projects. Currently however, interest rates have come down with the Overnight Bank Borrowing rate that RBI offers at 6.50%. This is still however significantly above that of China, and has the dual impact of keeping the India Rupee artificially inflated thereby putting Indian exports at a disadvantage.
Thus it is clear that Chinese inputs: raw material, energy, industrial capital and financial capital are all more competitive then Indias. They are in fact some of the most competitive in the globe leaving no surprise that China is the dominant steel manufacturer, and combined with tremendous steel consumption within China itself there is not doubt that Chinese steel industry is the foremost in the globe.
Share News
Please Login to place a comment
Login Now
-
LATEST
-
POPULAR